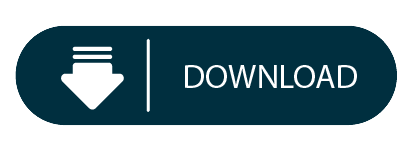
The fishbone (or Ishikawa) diagram is another way to visualize your 5-why analysis, and allows you to classify your analysis into broad categories. Part 3 of a series on the five-whys. More information: An Introduction to 5-why, 5-why Analysis using a Fishbone Diagram and The Weaknesses of 5-Why. A fishbone diagram, also known as Ishikawa diagram or cause and effect diagram, is a tool used to visualize all the potential causes of a problem in order to discover the root causes. The fishbone diagram helps one group these causes and provides a structure in which to display them.
- How To Use Ishikawa Diagram
- Ishikawa Diagramme
Ishikawa diagram |
---|
One of the Seven Basic Tools of Quality |
---|
First described by | Kaoru Ishikawa |
---|
Purpose | To break down (in successive layers of detail) root causes that potentially contribute to a particular effect |
---|
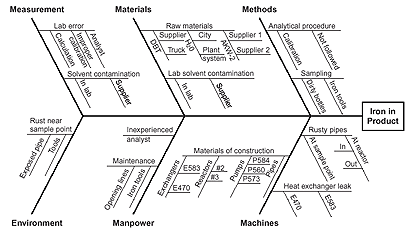
Ishikawa diagrams (also called fishbone diagrams, herringbone diagrams, cause-and-effect diagrams, or Fishikawa) are causal diagrams created by Kaoru Ishikawa that show the potential causes of a specific event.[1]
Common uses of the Ishikawa diagram are product design and quality defect prevention to identify potential factors causing an overall effect. Each cause or reason for imperfection is a source of variation. Causes are usually grouped into major categories to identify and classify these sources of variation.
Overview[edit]
Sample Ishikawa diagram shows the causes contributing to problem.
The defect is shown as the fish's head, facing to the right, with the causes extending to the left as fishbones; the ribs branch off the backbone for major causes, with sub-branches for root-causes, to as many levels as required.[2]
Ishikawa diagrams were popularized in the 1960s by Kaoru Ishikawa,[3] who pioneered quality management processes in the Kawasaki shipyards, and in the process became one of the founding fathers of modern management.
The basic concept was first used in the 1920s, and is considered one of the seven basic tools of quality control.[4] It is known as a fishbone diagram because of its shape, similar to the side view of a fish skeleton.
Mazda Motors famously used an Ishikawa diagram in the development of the Miata (MX5) sports car.[5]
Advantages[edit]
- Highly visual brainstorming tool which can spark further examples of root causes
- Quickly identify if the root cause is found multiple times in the same or different causal tree
- Allows one to see all causes simultaneously
- Good visualization for presenting issues to stakeholders
Disadvantages[edit]
- Complex defects might yield a lot of causes which might become visually cluttering
- Interrelationships between causes are not easily identifiable[6]
Root causes[edit]
Root-cause analysis is intended to reveal key relationships among various variables, and the possible causes provide additional insight into process behavior.
The causes emerge by analysis, often through brainstorming sessions, and are grouped into categories on the main branches off the fishbone. To help structure the approach, the categories are often selected from one of the common models shown below, but may emerge as something unique to the application in a specific case.
Each potential cause is traced back to find the root cause, often using the 5 Whys technique.
Typical categories include:
The 5 Ms (used in manufacturing)[edit]
Originating with lean manufacturing and the Toyota Production System, the 5 Ms is one of the most common frameworks for root-cause analysis:[7]
- Man / mind power (physical or knowledge work, includes: kaizens, suggestions)
- Machine (equipment, technology)
- Material (includes raw material, consumables, and information)
- Method (process)
- Measurement / medium (inspection, environment)
These have been expanded by some to include an additional three, and are referred to as the 8 Ms:[8]
- Mission / mother nature (purpose, environment)
- Management / money power (leadership)
- Maintenance
How To Use Ishikawa Diagram
The 8 Ps (used in product marketing)[edit]
This common model for identifying crucial attributes for planning in product marketing is often also used in root-cause analysis as categories for the Ishikawa diagram:[8]
- Product (or service)
- Price
- Place
- Promotion
- People (personnel)
- Process
- Physical evidence (proof)
- Performance
The 8 Ps are primarily used in product marketing.
The 4 Ss (used in service industries)[edit]
An alternative used for service industries, uses four categories of possible cause:[9]

- Surroundings
- Suppliers
- Systems
- Skill
See also[edit]
Ishikawa Diagramme
References[edit]
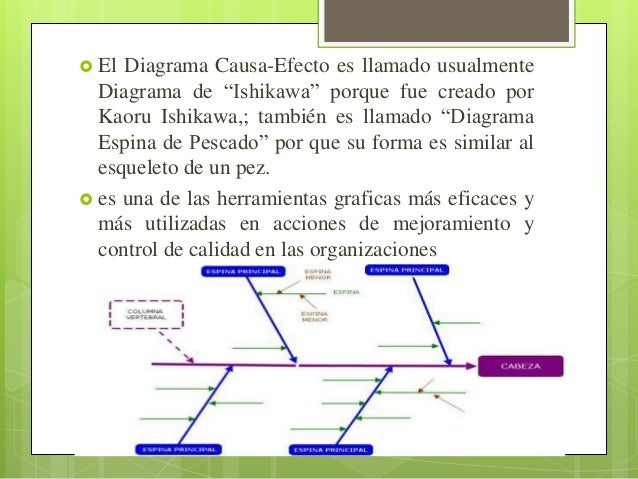
- ^Ishikawa, Kaoru (1968). Guide to Quality Control. Tokyo: JUSE.
- ^Ishikawa, Kaoru (1976). Guide to Quality Control. Asian Productivity Organization. ISBN92-833-1036-5.
- ^Hankins, Judy (2001). Infusion Therapy in Clinical Practice. p. 42.
- ^Tague, Nancy R. (2004). 'Seven Basic Quality Tools'. The Quality Toolbox. Milwaukee, Wisconsin: American Society for Quality. p. 15. Retrieved 2010-02-05.
- ^Frey, Daniel D.; 1943-, Fukuda, S. (Shūichi); Georg., Rock (2011). Improving complex systems today : proceedings of the 18th ISPE International Conference on Concurrent Engineering. Springer-Verlag London Ltd. ISBN978-0857297990. OCLC769756418.CS1 maint: numeric names: authors list (link)
- ^'How to use the fishbone diagram to determine data quality root causes'. LightsOnData. 2018-12-05. Retrieved 2018-12-15.
- ^Weeden, Marcia M. (1952). Failure mode and effects analysis (FMEAs) for small business owners and non-engineers : determining and preventing what can go wrong. ISBN0873899180. OCLC921141300.
- ^ abBradley, Edgar (2016-11-03). Reliability engineering : a life cycle approach. ISBN978-1498765374. OCLC963184495.
- ^Dudbridge, Michael (2011). Handbook of Lean Manufacturing in the Food Industry. John Wiley & Sons. ISBN978-1444393118. OCLC904826764.
Further reading[edit]
Wikimedia Commons has media related to Ishikawa diagrams. |
- Ishikawa, Kaoru (1990); (Translator: J. H. Loftus); Introduction to Quality Control; 448 p; ISBN4-906224-61-XOCLC61341428
- Dale, Barrie G. et al. (2007); Managing Quality 5th ed; ISBN978-1-4051-4279-3OCLC288977828
Retrieved from 'https://en.wikipedia.org/w/index.php?title=Ishikawa_diagram&oldid=1010409237'
This cause-and-effect diagram example was redesigned from the Wikimedia Commons file: Ishikawa Fishbone Diagram.svg. [commons.wikimedia.org/ wiki/ File:Ishikawa_ Fishbone_ Diagram.svg]
'Ishikawa diagrams (also called fishbone diagrams, herringbone diagrams, cause-and-effect diagrams, or Fishikawa) are causal diagrams created by Kaoru Ishikawa (1968) that show the causes of a specific event. Common uses of the Ishikawa diagram are product design and quality defect prevention to identify potential factors causing an overall effect. Each cause or reason for imperfection is a source of variation. Causes are usually grouped into major categories to identify these sources of variation. The categories typically include
- People: Anyone involved with the process
- Methods: How the process is performed and the specific requirements for doing it, such as policies, procedures, rules, regulations and laws
- Machines: Any equipment, computers, tools, etc. required to accomplish the job
- Materials: Raw materials, parts, pens, paper, etc. used to produce the final product
- Measurements: Data generated from the process that are used to evaluate its quality
- Environment: The conditions, such as location, time, temperature, and culture in which the process operates' [Ishikawa diagram. Wikipedia]
The example 'Ishikawa fishbone diagram' was created using the ConceptDraw PRO software extended with the Seven Basic Tools of Quality solution from the Quality area of ConceptDraw Solution Park.